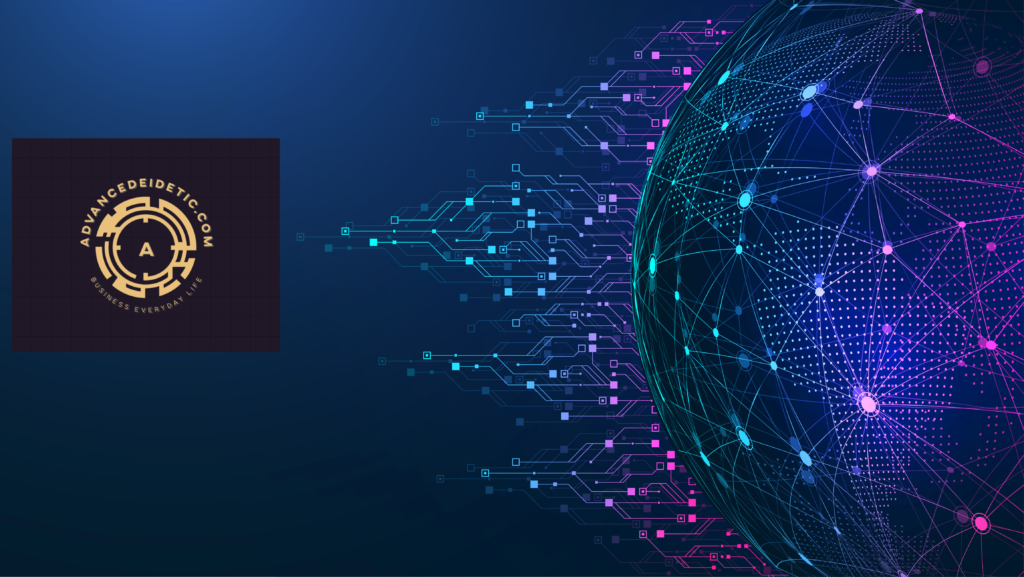
Lean Operations: Implementing Lean Methodologies to Make Business Operations Efficient and Effective
In the competitive landscape of modern business, efficiency is paramount. Companies that can streamline their operations and eliminate waste are better positioned to thrive in a market where agility and responsiveness are key. Lean methodologies, rooted in the principles of continuous improvement and waste reduction, offer a proven framework for businesses aiming to optimize their operations. This guide delves into the core concepts of lean operations, providing actionable insights on how to implement these methodologies to make your business more efficient and effective.
Understanding Lean Methodologies
Before diving into the practical steps of implementing lean methodologies, it’s essential to grasp the foundational concepts that drive lean thinking. At its core, lean is about delivering maximum value to the customer with the least amount of waste. This philosophy, originally developed in the manufacturing sector, has since been adapted across various industries due to its universal applicability.
The Five Principles of Lean
The five principles of lean—value, value stream, flow, pull, and perfection—serve as the backbone of any lean initiative. Understanding and applying these principles can transform how a business operates.
1. Value: The first principle focuses on defining what is valuable from the customer’s perspective. This helps in identifying the products or services that are worth investing in and eliminating those that don’t contribute to customer satisfaction.
2. Value Stream: Mapping the value stream involves analyzing all the steps involved in bringing a product or service to the customer. This step is crucial for identifying areas of waste that can be eliminated.
3. Flow: Once the value stream is mapped, the goal is to ensure that the processes flow smoothly without interruptions or delays. This involves removing bottlenecks and ensuring that each step in the process adds value.
4. Pull: Lean operations rely on a pull-based system, where production is driven by customer demand rather than forecasted demand. This reduces the risk of overproduction and excess inventory.
5. Perfection: The final principle of lean is the pursuit of perfection through continuous improvement. Businesses should constantly seek ways to refine their processes, reduce waste, and enhance value delivery.
Implementing Lean in Business Operations
With a solid understanding of lean principles, the next step is to implement these methodologies within your business operations. This requires a strategic approach that involves everyone in the organization, from top management to frontline employees.
Leadership Commitment: Driving the Lean Culture
For lean methodologies to be successful, leadership must be fully committed to the process. This means not only providing the necessary resources and support but also leading by example. Leaders should embody the lean philosophy, demonstrating a commitment to continuous improvement and waste reduction.
Employee Engagement: Empowering the Workforce
Lean operations thrive on the active involvement of employees at all levels. Engaging employees in the process improvement initiatives ensures that they are motivated to identify inefficiencies and suggest improvements. Training programs, workshops, and open communication channels are essential tools for fostering a lean culture.
Lean Tools and Techniques
Implementing lean methodologies involves the use of specific tools and techniques designed to streamline operations and eliminate waste. These tools provide a structured approach to problem-solving and process improvement.
5S Methodology: Organizing the Workplace
The 5S methodology—Sort, Set in order, Shine, Standardize, and Sustain—is a foundational lean tool that helps organize the workplace for maximum efficiency. By systematically organizing the workspace, businesses can reduce waste, improve productivity, and create a safer work environment.
1. Sort: Eliminate unnecessary items from the workspace, keeping only what is essential.
2. Set in Order: Arrange necessary items in a way that maximizes efficiency.
3. Shine: Regularly clean and maintain the workspace to prevent issues.
4. Standardize: Establish standards for organizing and maintaining the workspace.
5. Sustain: Continuously maintain and improve the organization of the workspace.
Kaizen: The Power of Continuous Improvement
Kaizen, a Japanese term meaning “change for the better,” is a lean tool focused on continuous improvement. Kaizen involves making small, incremental changes that lead to significant improvements over time. By encouraging all employees to participate in Kaizen activities, businesses can foster a culture of continuous improvement that drives long-term success.
Measuring the Impact of Lean Operations
Once lean methodologies are implemented, it’s crucial to measure their impact on business operations. This involves tracking key performance indicators (KPIs) to assess whether the lean initiatives are delivering the desired results.
Key Performance Indicators for Lean
KPIs are essential for evaluating the effectiveness of lean operations. Common KPIs include cycle time, lead time, defect rates, and customer satisfaction. By regularly monitoring these metrics, businesses can identify areas for improvement and make data-driven decisions.
The Role of Feedback in Continuous Improvement
Feedback plays a critical role in lean operations. Regular feedback from employees, customers, and stakeholders provides valuable insights into how well the lean initiatives are working. This feedback should be used to refine processes, address issues, and continuously improve operations.
Overcoming Challenges in Lean Implementation
While lean methodologies offer significant benefits, implementing them is not without challenges. Businesses must be prepared to address potential obstacles that can hinder the success of lean operations.
Resistance to Change: Managing the Human Element
One of the most common challenges in lean implementation is resistance to change. Employees who are accustomed to traditional ways of working may be hesitant to embrace new processes. To overcome this resistance, it’s important to communicate the benefits of lean, involve employees in the decision-making process, and provide the necessary training and support.
Sustaining Lean Operations: Avoiding Regression
Sustaining lean operations over the long term requires ongoing commitment and vigilance. Businesses must ensure that the lean culture is deeply ingrained in the organization and that there are mechanisms in place to prevent regression. This includes regular audits, continuous training, and a focus on long-term goals.
Conclusion
Implementing lean methodologies is a powerful strategy for making business operations more efficient and effective. By understanding the principles of lean, engaging employees, and using the right tools and techniques, businesses can achieve significant improvements in productivity, quality, and customer satisfaction. However, it’s important to remember that lean is not a one-time initiative—it’s a continuous journey that requires ongoing effort and commitment. By embracing lean operations, businesses can position themselves for long-term success in an increasingly competitive market.
Call to Action:
Ready to take your business operations to the next level? Join our community at AdvanceEidetic.net to access exclusive resources, expert insights, and actionable strategies for implementing lean methodologies. Contact Us today and start transforming your business for long-term success!